|
Operation
& Use
|
|
|
|
|
|
|
|
|
|
|
|
|
|
|
|
|
|
|
|
|
|
|
|
|
|
|
|
|
|
 |
|
|
Operation
Loading
and unloading of the kiln is performed by the means of rail carriage
platform. The patented distance vented stickers render possible longitudinal
ventilation of the stacking, control of air movement including better
drainage of moisture from the wood surface, and at the same time their
design enables ventilation through the stickers as well as on the
contacts of the wood with the stickers which eliminate sticker stains,
normally causing defective coloration of the wood. The desired climate
can be maintained in the drying kiln with its volume of 22 m3
without any problems. This also applies to the ventilation and the
so called air break-though the whole stack by-passing all elements,
and to the appropriate preparation of the quantity of air for drying.
The air is dried or moistened immediately after its exit from the
stacking in the so-called power house of the kiln. With
the appropriate regulation of drying schedules
the required air climate in the kiln is gradually obtained and can
be regulated very accurately. Thus the wood is drying steadily and
evenly, without great changes of climate. In case freshly sawn wood
has to be dried, the gradual drying of wood passes from the stage
of pre-drying to the stage of drying, conditioning and finally, the
cooling process. The drying temperatures of up to 50°C ensure
drying without the risks which are caused by aggressive drying at
high temperatures (defects in the form of various cracks, splits,
encrustation, and color-changes). Drying at temperatures up to 50°C
preserves the quality of the wood. Due to steady non-aggressive drying
the moisture gradient in wood can reach the highest quality.
The
placing of separate components is well chosen and tested. The vent
for pre-drying enables a adequate exchange of air. A temperature
condensation device makes exceptional use of the system, taking
a part of the saturated cooled air from the stacking and dehumidifying
and heating it. By means of the vent for a partial exchange of air
a part of the saturated air in the kiln is exchanged for fresh air.
Adequate air flow in the kiln is generated by least two special
axial ventilators. The moisturizing device uses soft decalcified
pre-heated water for the occasionally required moisturizing. The
water is not sprayed over the wood but into the circulating air
in the drying area. Thus the air enters the stacking properly prepared.
By a specific climate in the complex drying kiln, wood is dried
to the desired final moisture content in a short time. An electronic
psychrometer is placed in the drying kiln to monitor the moisture
content of the wood. Monitoring moisture content in wood is performed
by four measuring sensors. The sensor temperatures have been pre-tested.
The drying equipment can be managed by the automatic remote control
through a computer, on which drying in 32 units can be controlled.
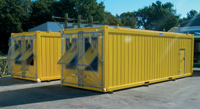
|
|
Thorough
preparation of the automated drying kiln management optimizes the
drying process and facilitates the whole process. A graphical display
of the drying process is recorded by the computer.
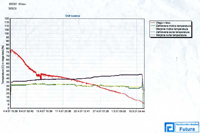
We can monitor the current situation in the kiln at any time without
having to leave the office or our working place.
Use
The Futura drying unit is constructed in the form of a standard
mobile container. It can be delivered by any standard transport
means used in container transport, which represents the drying kiln
Futura as a mobile device independent on surrounding conditions.
When delivered to the user, the drying kiln unit is positioned on
the desired place, connected to an electric supply and ready to
use.
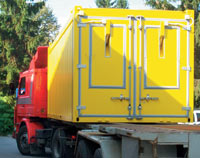
>The
complex drying kiln Futura regarding its capacity is not intended
only for small users of dry wood. Several Futura drying units enable
bigger availability of dry wood and therefore enable such users
drying of different types and dimensions of wood, smaller storage
areas and more flexibility on further production. Due to the concept
of the drying kiln Futura the drying itself is very steady and of
quality throughout the entire drying area, therefore deviations
and irregularities are minimal.
>The drying kiln management is going
through the computer, which can be placed in the next-door building.
The user only has to specify the type, thickness and desired final
moisture content, the rest is done automatically by the drying kiln.
|
|